-
BOXERgeom is an innovative product based on a revolutionary, next generation Digital Geometry modelling kernel.
-
Design optimization freed from the constraints of BREP NURBS.
-
Understand & mitigate in-service geometry degradation & wear, to better manage life & MRO costs.
-
Coupled in parallel to BOXERmesh which reliably delivers a solvable mesh whatever the geometry.
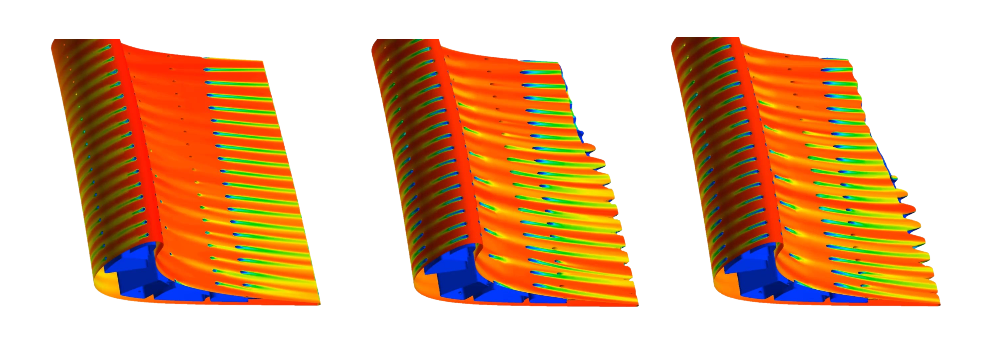
BOXERgeom uses Digital Geometry kernel capabilities to provide robust boolean operations, geometry editing and sculpting. All in an entirely topology-independent and unconstrained manner- and all coupled to the fast and automated meshing of BOXERmesh. This avoids the usual issues associated with mesh deformation, providing fast and robust enviroment for design edits coupled to physical modelling.
BOXERgeom can alter a geometric surface in response to an arbitrary surface scalar value such as temperature, pressure, x-location, particle impact frequency etc. The surface can be made to move outward (add material) or inward (remove material) to model particle build-up, icing, erosion or burn-out in response to the local scalar value.
- In-service part degradation
- Erosion
- Corrosion
- Particulate Build Up
The unique capability of BOXERgeom allows the user to deform geometries using solver data.
- Import and mesh the new or manufactured part geometry.
- Obtain data such as corrosion rate, erosion rate, particulate flow from simulation software of your choice.
- Using BOXERgeom, apply data to deform geometry (predict erosion, corrosion and particulate build up).
- Mesh the generated geometry and simulate to understand in-service part performance.
- Use the updated data from simulation to further deform and update geometry through part life.
Boiler Tube Fouling
Choke Valve Erosion
Particle flow data was used on the choke valve geometry to model erosion. The eroded geometry can be meshed and exported for analysis to identify failure point for the part.
Level-set A-B shape morphing allows users to generate shape change for a geometry by smoothly morphing the entire geometry envelope from a source (Shape ‘A’) to a target (Shape ‘B’). All intermediate shapes which are an evolution of A-to-B are directly available for meshing and model creation. The morphing process runs in parallel and can therefore accommodate large and detailed models with large variations in length scale.
Understand Part Degradation
The A to B morph level set allows visualisation and analysis of components as they age. Import geometry of new and in-service/ failed component and use the morph tool to visualize how the component may have degraded over time.The morph level set tool will allow users to mesh and export geometry at intermediate stages of the morph for analysis.
Smoothly deform shapes based on the displacement of a lattice of control points which surround and enclose the geometry.
The user interface for setting up and moving the control points in BOXERgeom are based on direct interaction with the graphical scene using drag handles, and the geometry updates in near-real-time following a change in control point position.
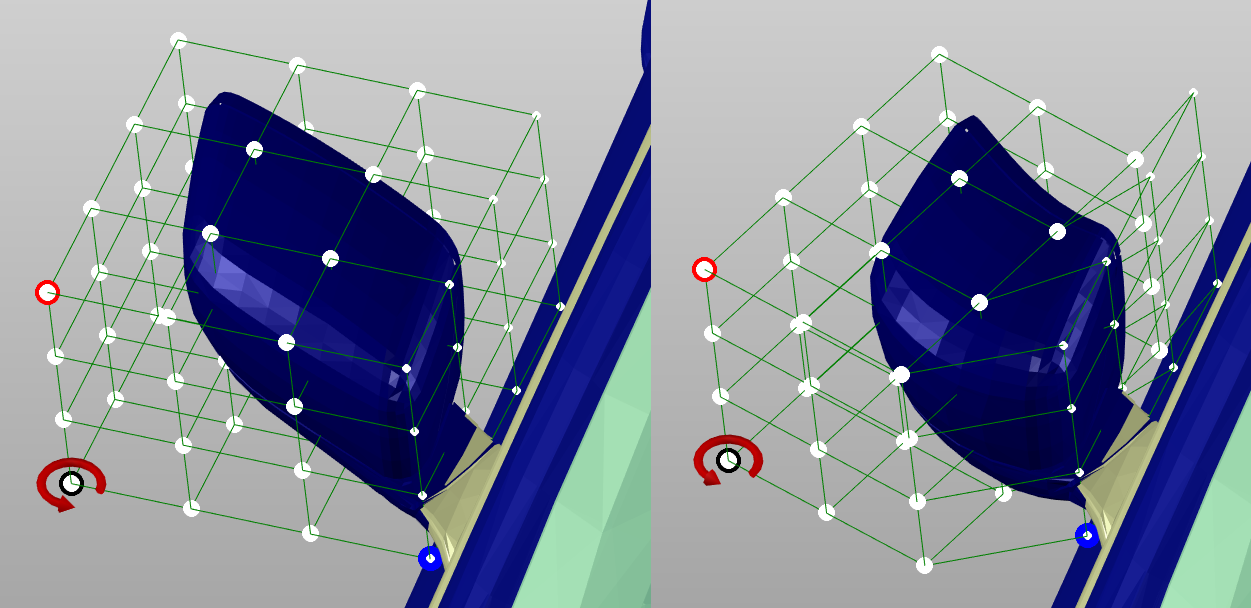